Blue Collar Customs
A shoebox Ford is welded up to a chassis jig to have its suspension redone.
Keeping busy in times of crisis
Words+ photos: Mike Blanchard
Winter is traditionally the time to rebuild or construct cars so they can be ready to race or drive in the balmy months. Shop doors all over the world are closed up with the heaters on and the sparks flying as craftsmen and women work to make dreams come true.
One of the peculiarities of this year of COVID shutdowns is that while some businesses are facing shutdown, others are going gangbusters. Blue Collar Customs in Sacramento has been around for 20 years or so building hot rods and customs. They are known for their chassis building and panel work, and at the moment the shop is jammed full.
In the doorway is a ’65 Mustang convertible getting flares. Next to it is a ‘48 International truck. Under the lift is a custom Shoebox Ford in bare steel. A couple cars over an Allard sports car is having its body mounted. Up on the big chassis table is a ’35 Ford pickup that is being rebuilt from the ground up with a new chassis, independent front suspension and fuel-injected big-block power. Every inch of two buildings is taken up with work. These guys are up to their eyes in it.
Blue Collar has built award-winning customs and hot rods for rock stars and football players. The shop is proud of this, but it is their commitment to quality that has brought a steady stream of customers. Custom car builders often work in a specific style, and if you want something outside of that they will politely suggest a different shop. Blue Collar is somewhat unique in that they tackle a broad range of jobs from traditional hot rods and slammed customs to four-wheel-drive trucks, muscle cars and sports cars.
A slammed ‘65 Dodge Sweptline sits low.
“We get excited about good fabrication,” says co-owner Scott Mugford. “The style may not be exactly what we want. We can bend a little on the style but we won’t bend on the quality.”
Each one of these jobs is unique. There is little of the cookie-cutter in this line of work. Take the International pickup: It has had most of the lower third of the body re-fabricated inside and out. All the little inner bracketing and panels that you never see have been painstakingly remade and installed. If you didn’t know you would think you were looking at factory work.
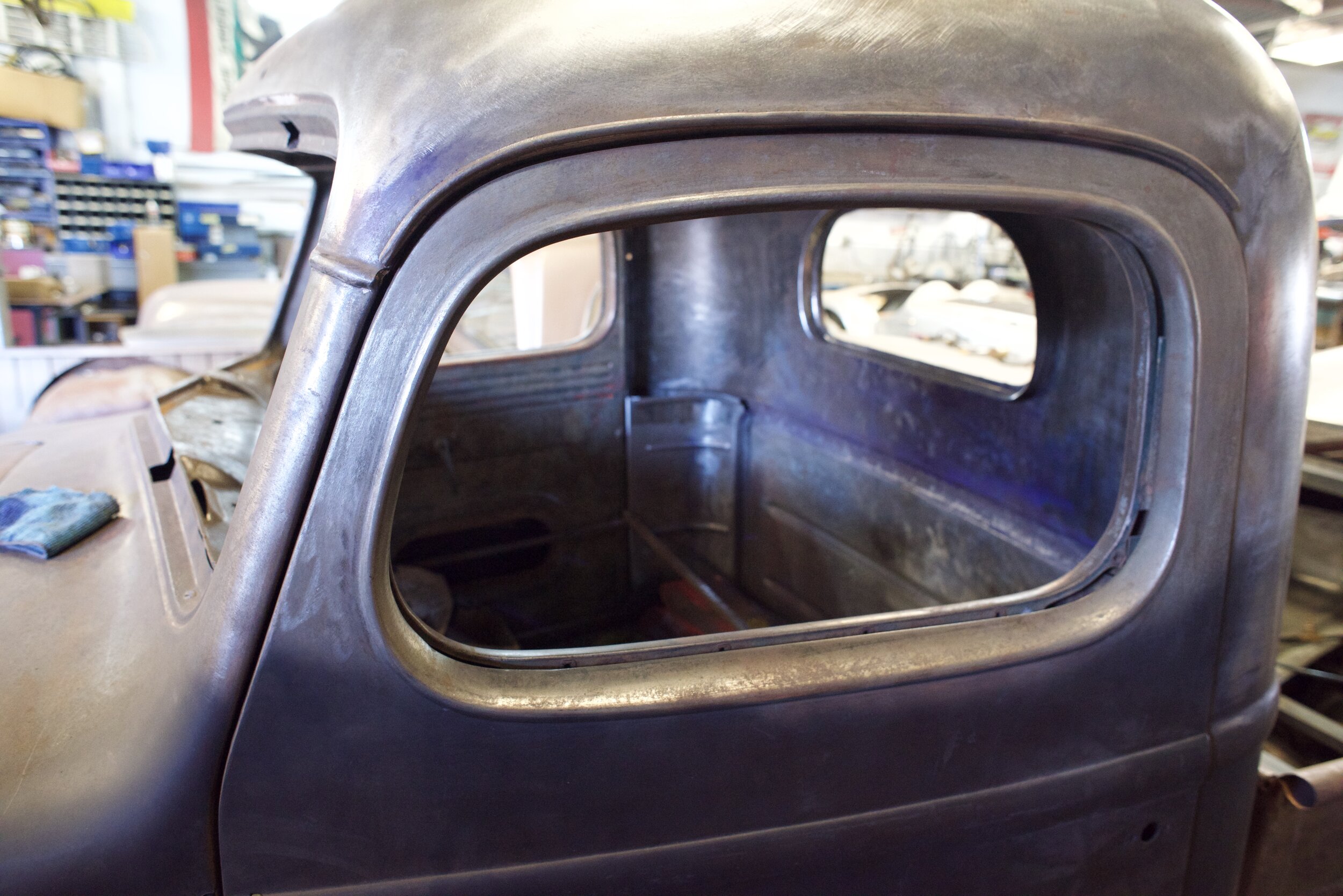
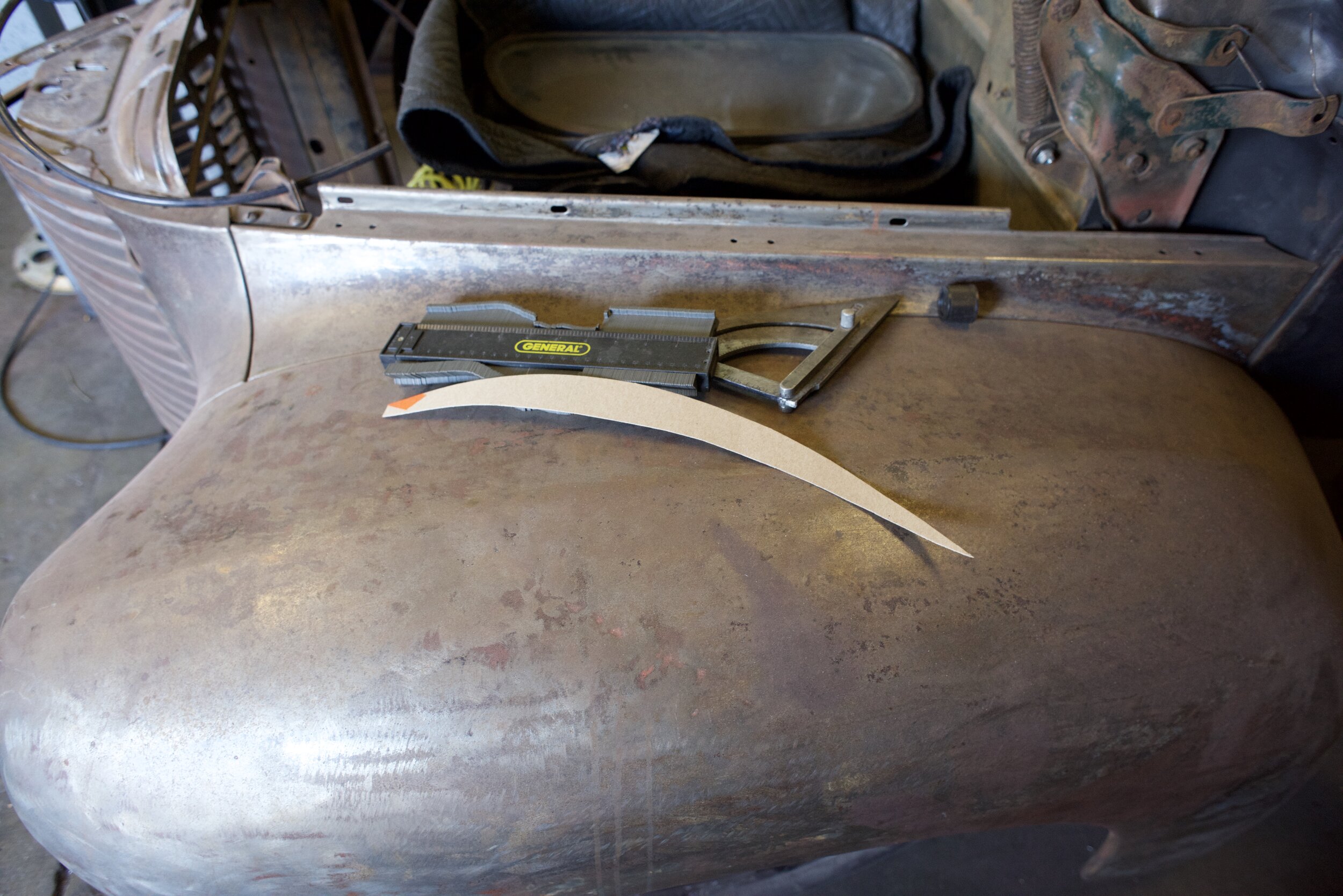
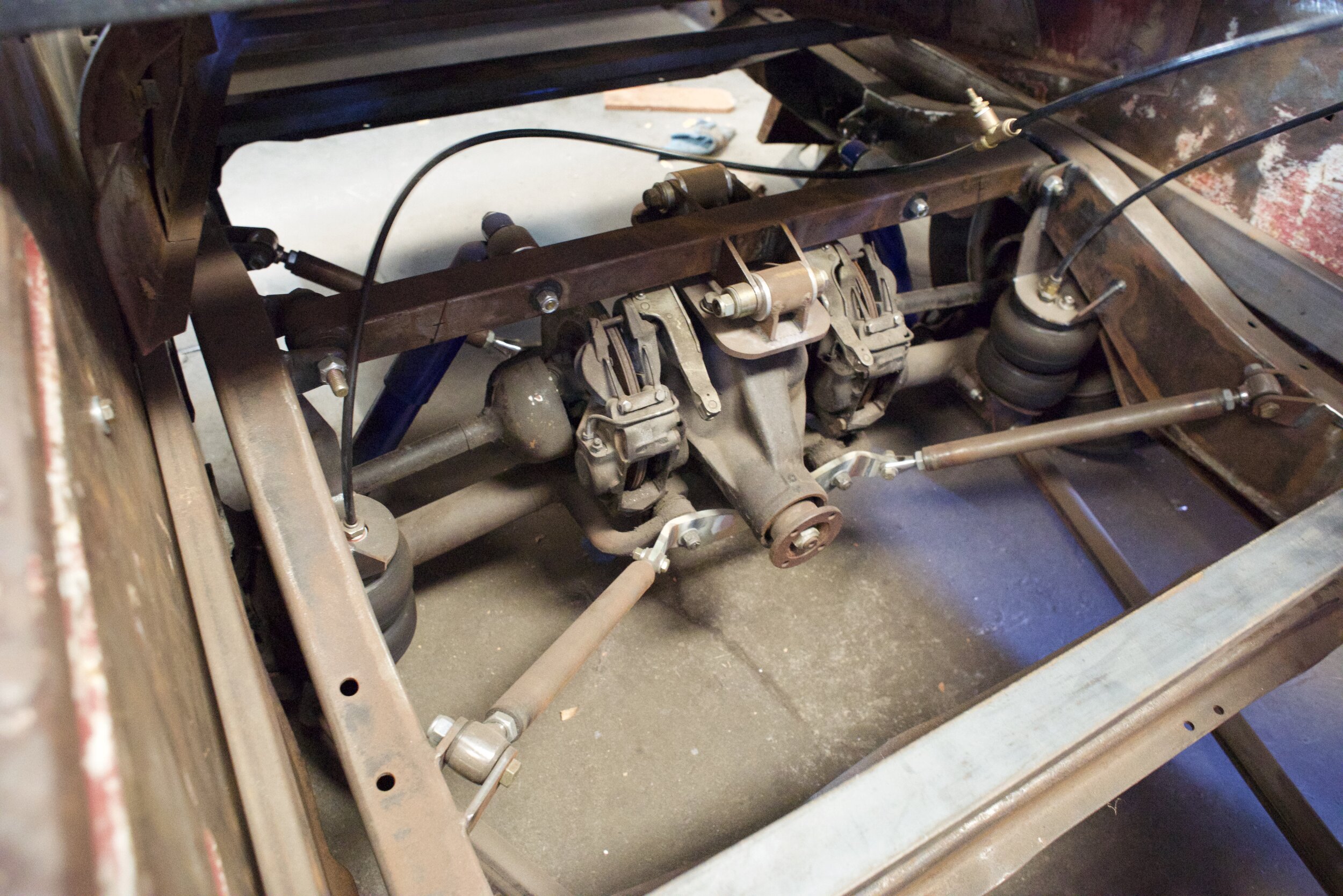
When it came in, the upper-rear portion of the cab was caved in. Fabricator Toby Stephen patiently brought it back to its correct shape and cleaned everything up, making new body panels as needed. The chassis has been rebuilt with Jaguar independent suspension front and rear. All the suspension arms and linkages have been scratch-built. It’s what the customer wanted.
The customer has just asked for the rear window to be made to roll down. Add it to the list. Blue Collar has well over 400 hours in the truck and many more to go before it will roll out the door. When it’s done the truck will have vintage looks and sports car handling.
One of the most unique jobs in the shop at the moment is the ’51 Allard J-2. The brainchild of Sydney Allard, the car is a mix of English body and chassis with a big, stonking American V-8.
They typically came with Ford Flathead V-8, Olds, Cadillac or Chrysler engines, but when purchased this car had an early Buick Nailhead bolted up. Given that the Nailhead came out after 1951 it’s a cinch the car has had at least one engine swap. But all that is academic; the important bit is that Allards were the forerunner of the Sunbeam Tiger and the Cobra. And there are not a lot of them. That makes this a rather historic car.
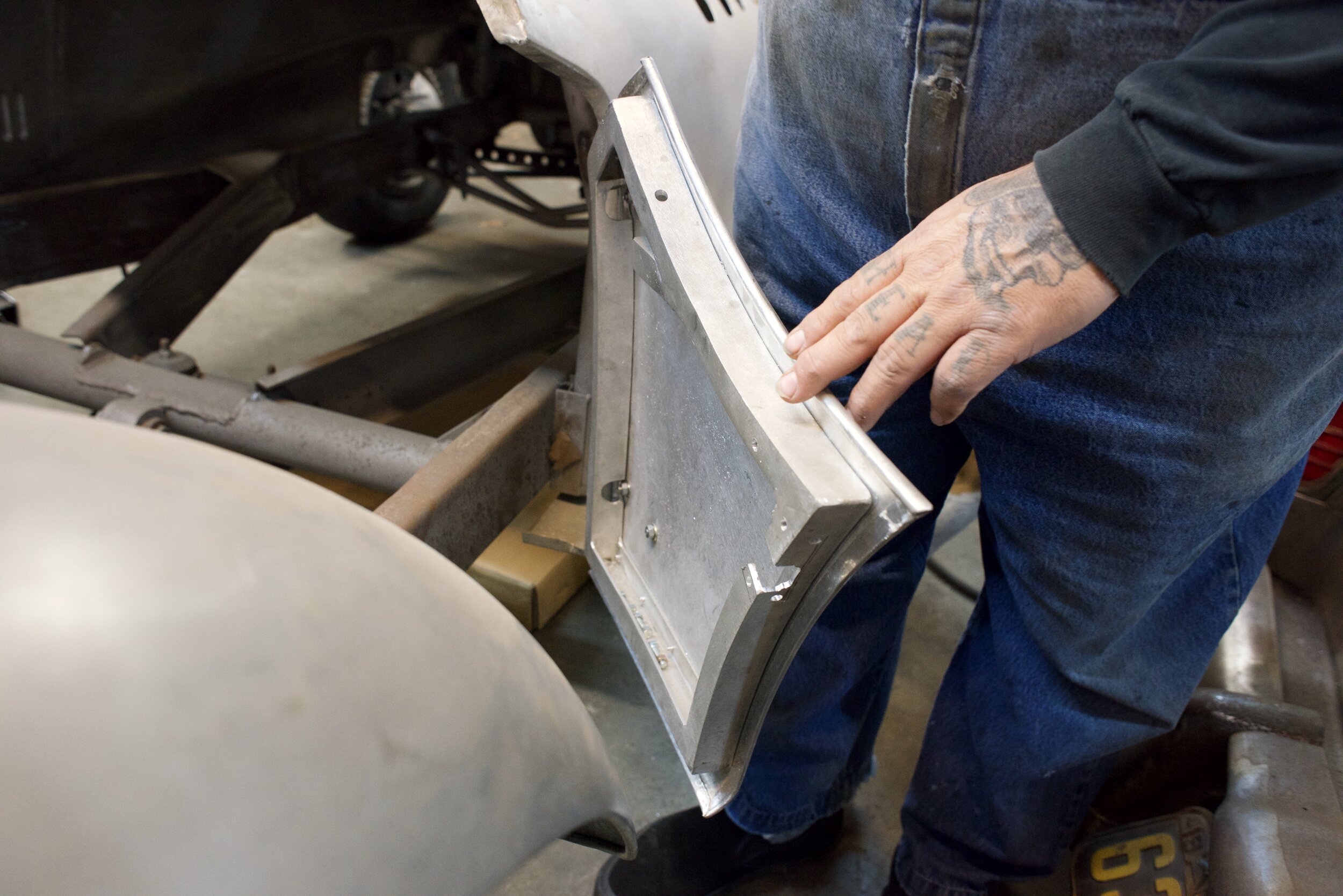
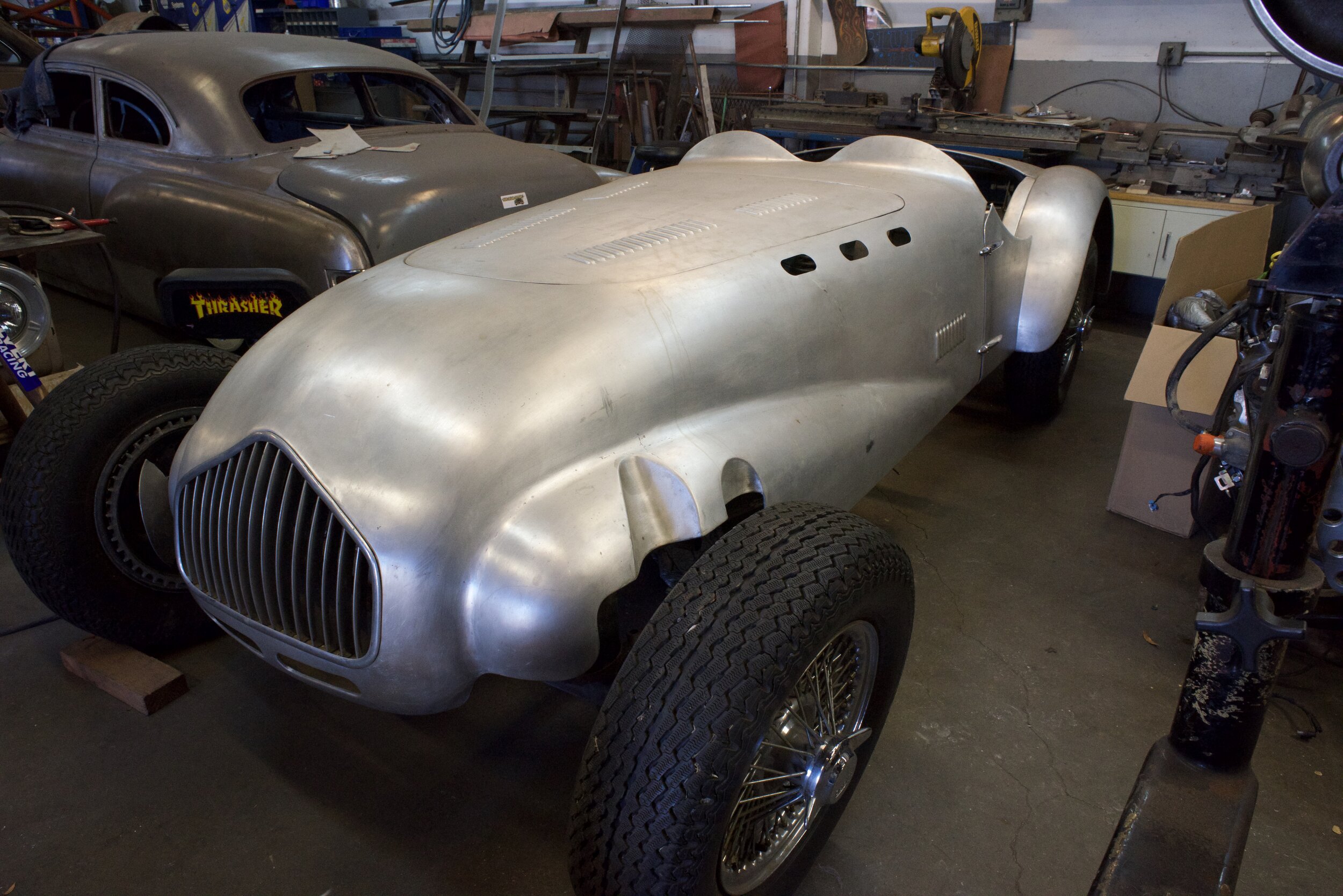
Despite an idiosyncratic (read sketchy) front suspension with the beam axle hinged in the middle, in their day they were a fairly competitive race car. “On paper the thing shouldn’t work,” says Mugford. “It’s a death machine. But in practice it works pretty good.”
This car was driven and raced throughout the ‘50s and wrecked in ’58. In the early ‘60s Allard supplied a new body for it but the body was never mounted. Because these cars were basically handmade, nothing is interchangeable in the way we think of parts now. “The body is weird,” says Mugford. “It was set way back and the doors were two inches too long.” Of course they were. Allard made the body without having the actual car on hand.
Originally the rear of the body from the doors back was mounted so that the rear wheels were up against the front of the wheel arch. Blue Collar repositioned the body so that the wheels are centered in the wheel arch with room for the suspension to work. Then they disassembled the doors, adjusted them to fit and fabricated door latches using Model A roadster assemblies. Everything is done with an eye to what is period correct and correct for the aesthetics of the car.
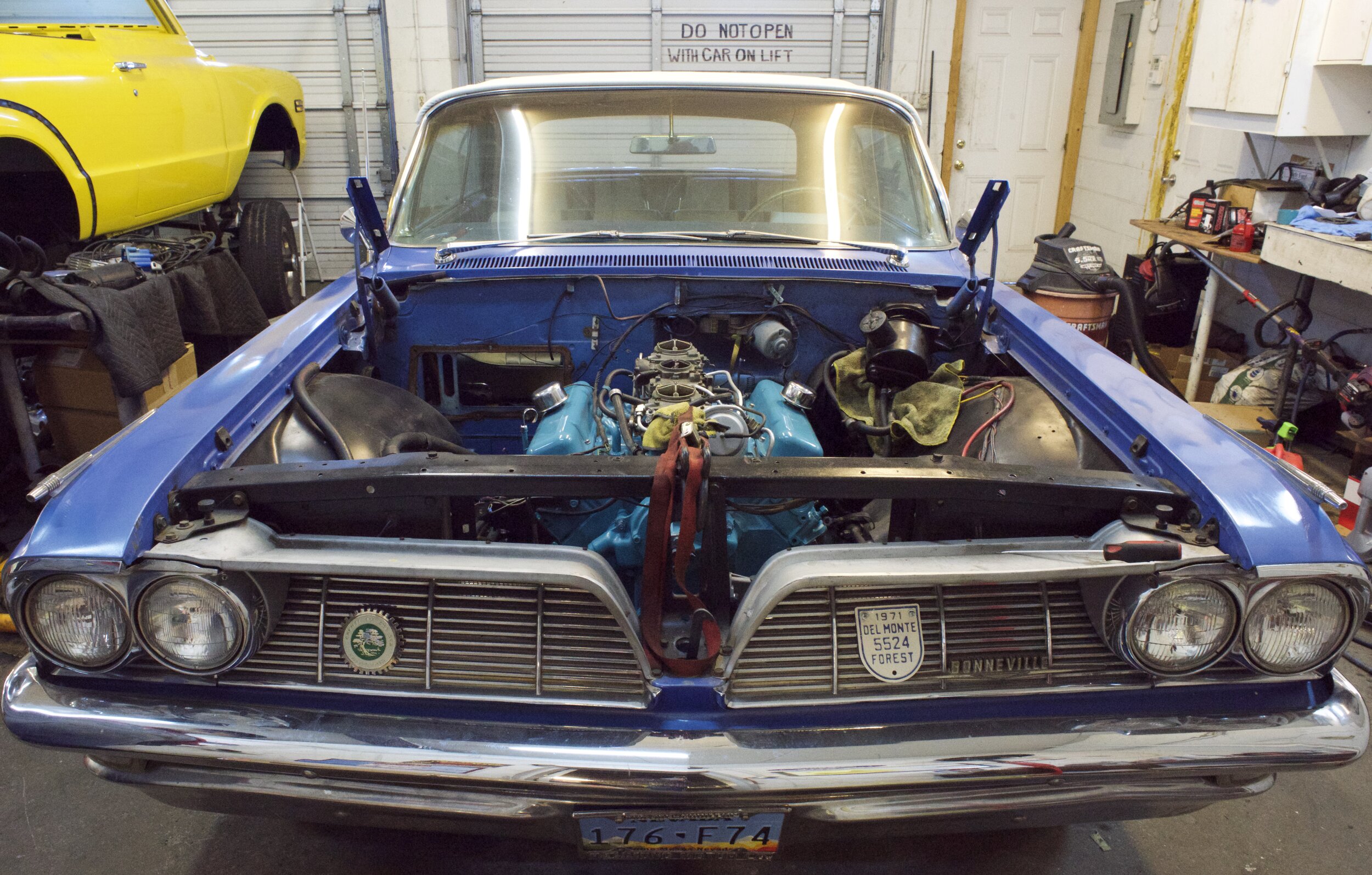
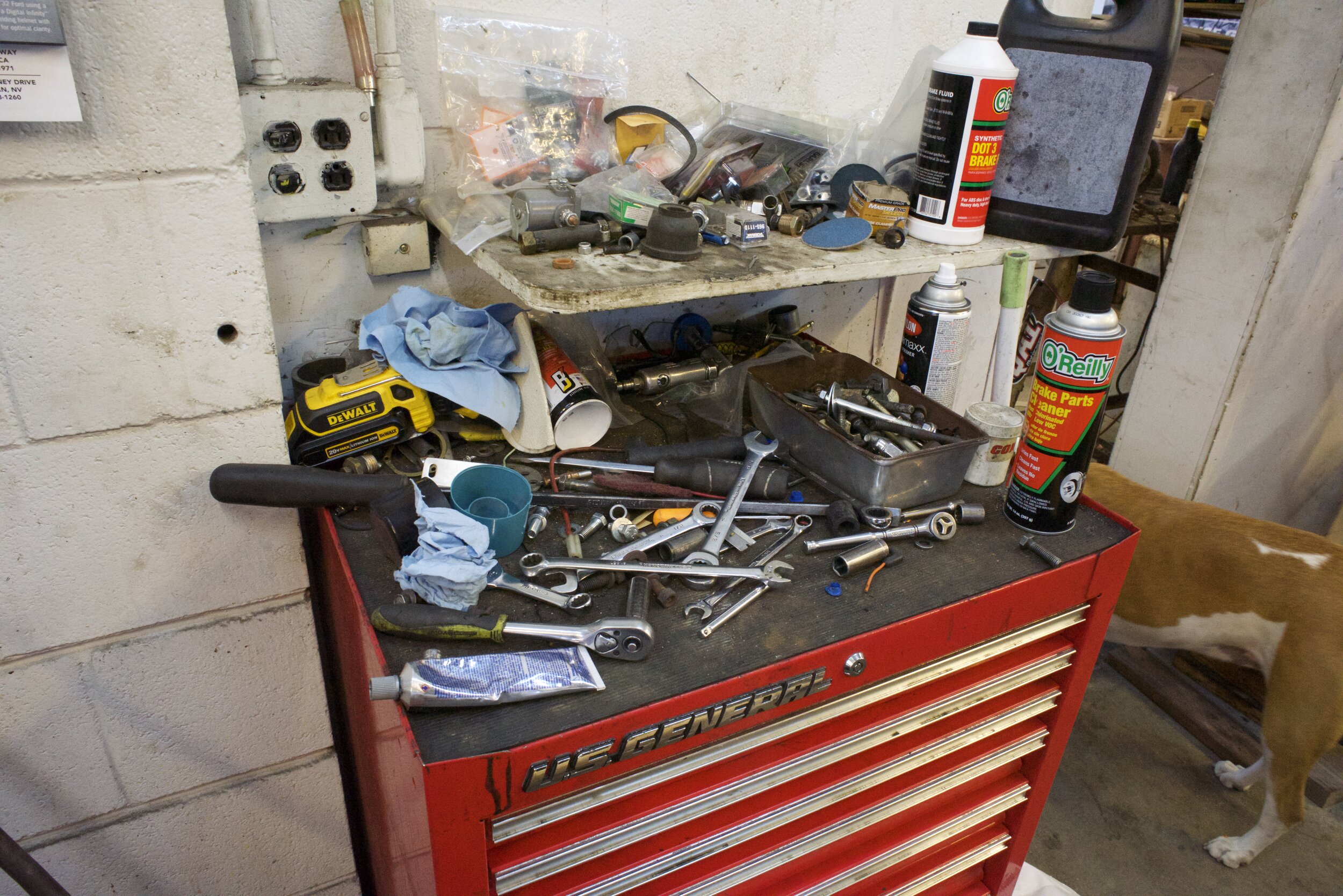
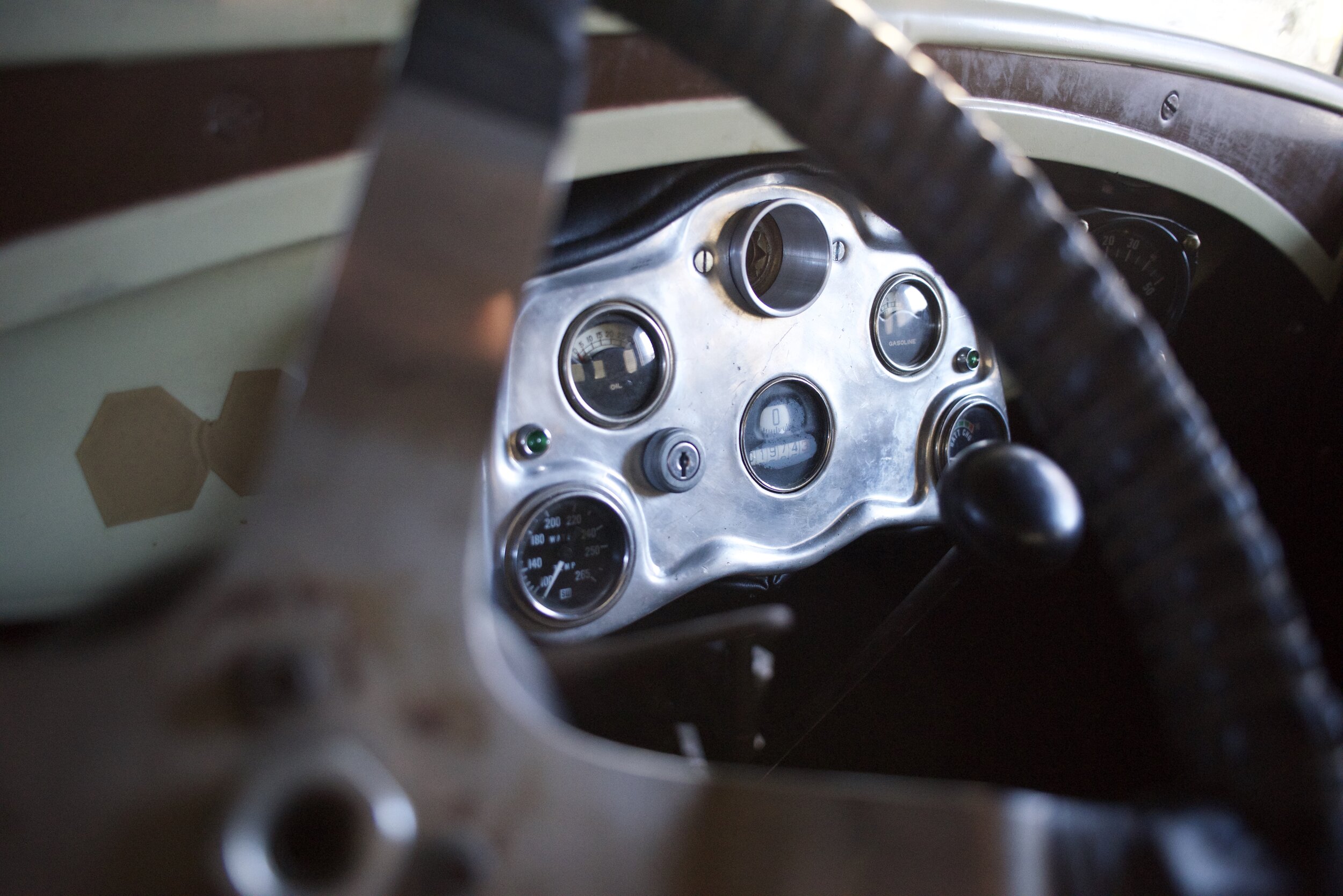
This is important. Shoddy work gets around, and a shop like this lives and dies on its reputation for quality. You will note in the photos a total lack of plastic filler. The panel work done in this shop is metal work. If a panel is too rusty or cannot be saved it is not covered over with filler. A new panel is fabricated to replace the damaged one. This is, perforce, an old-world ethic where the craftsman is preeminent. Only in this way can the work be done with credibility.
Customers commonly wait years for a big job to be finished. It’s not that the shop is wasting time. It is simply that this work takes time. You can’t rush making things by hand. And there is no easy or accurate way to estimate jobs like this, says Mugford. “It’s $80 per hour for as much as they can handle.”
Not all the work takes that long. Many customers bring their cars in to have small jobs done, slowly transforming the car as they have money to spend. In this business you need a good mix of short-term and long-term jobs to keep the lights on. And at Blue Collar the lights burn long into the night.
So, there is a little peek at what is going on in a shop on a quiet street in Sacramento.